Blog
Retrofits Legacy Boiler at West Texas Refinery with Modular Equipment
January 31, 2013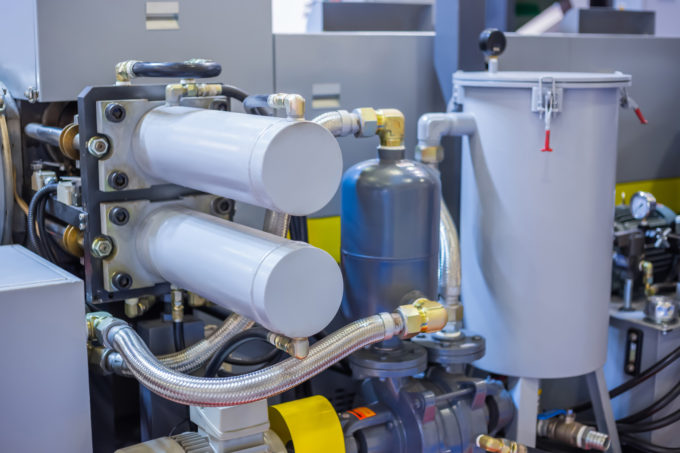
Principal Technology Inc., a provider of total system solutions for natural gas, refining, chemical, process and manufacturing facilities, improved the safety and operations of a West Texas gas processing plant through the modernization of a glycol reboiler burner and combustion controls. Operated by a large national gas processing company, the glycol reboiler is the fourth burner management system Principal Technology has retrofitted for the customer.
The existing equipment was a natural draft fired, dual burner, glycol reboiler with an outdated burner ignition system and primarily manual combustion controls. In addition to advanced age of the existing burners and controls, the equipment was also operationally inefficient due to the lack of accurate temperature control and flame management capabilities. Principal Technology’s solution for the out-of-date reboiler was a modular burner management system (BMS) specifically designed for the retrofit of legacy boilers, ovens, furnaces, and other fired equipment used in the process industry.
Principal Technology replaced the old equipment with modern forced draft burners, a control system and fuel train based on PTI’s modular platform including a burner management safety system with automated combustion control. The new system’s automatic ignition sequencing offers reliable flame safeguards and meets current NFPA safety standards. Principal Technology also added remote control allowing operators to start, stop and diagnose problems from the plant’s central control center. Operations were enhanced with automated temperature control to maintain a stable reboiler temperature and allow for consistent control of the process fluids.
“Unlike a traditional engineering approach to a BMS retrofit, which usually involves creating a completely new system specifically designed for a particular application, Principal Technology’s modular approach creates a custom BMS by applying individual modules to the application as needed,” said Matthew S. Hodson, P.E., president and CEO of Principal Technology. “The result is a BMS tailored to the customer’s exact needs but delivered more quickly because the component pieces are pre-engineered. In the case of the West Texas plant, from arrival onsite to the first fire of the reboiler took only four days. This allowed us to minimize down time while retrofitting the equipment and provide the customer a safer and much more efficient system.”
Principal Technology uses its modularization expertise to retrofit legacy equipment from fully or partially manual operation to completely automated systems. Having standardized the BMS into modular blocks, Principal Technology can adapt the components to create a unique BMS to meet the needs of any processing facility and complete installation and testing significantly faster than a standard engineered retrofit.
Ready to discuss a project?
Reach out to our team to get started
Principal Technology is a full service engineering firm with additional support for system integration, fabrication, sulfur recovery, amine treating, and a wide selection of turnkey solutions.
Call 214-239-3900 or send us a message.